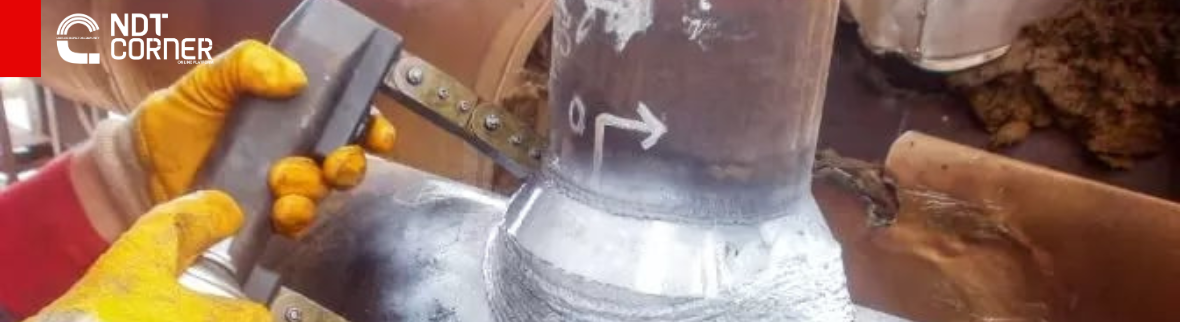
How does fatigue impact the POD for Magnetic Particle Inspection?
31 Jul 2023 Download PDF
Work hardening and fatigue are caused by physical processes and deformations imposed on a metal. For example:
- Plastic deformation
- Welding activities
- Repeated stress and strain on the material
As mild steel experiences work hardening and fatigue, the magnetic properties of the steel change. Let’s take a look at the kinds of changes you can expect.
Property Changes Due to Fatigue
When metal becomes fatigued, three significant properties change.
- Coercivity Increases – the metal becomes more resistant to changes in magnetization.
- Remanence Decreases – after the magnetizing force is removed, very little magnetism remains.
- Permeability (μ) Decreases – fatigued metal becomes more difficult to magnetize.
When discussing Permeability, it’s important to note that Permeability (µ) is a ratio – a function of B and H. That is, B = µH, where B = flux density in Gauss and H = magnetizing force in Oersteds. So, when μ decreases, the amount of magnetizing force remains the same and the codes still mandate a 30 Oersted value for B. H for AC yokes is fixed. As a result, there is only physical spacing to reduce magnetizing force.
This being said, it is important to be cognizant of the variables in order to get a result and maintain probability of Detection. B is generally overstated in the codes to a value that is three times that necessary. This results in spurious indications and a low probability of detection for Yoke MPI (i.e. around 44%).
To further illustrate the extent to which fatigue affects permeability, we’ve provided a visual representation below. What you’ll notice in this diagram is that the permeability of a cracked or fatigued material is approximately 30% less than the material in its original state.
When it comes to Magnetic Particle Inspection, changes in permeability have the most significant impact on POD.
But how does permeability impact the probability of detection when using MPI testing? Let’s take a look.
Impacts of Decreased Permeability on Magnetic Particle Inspection
Decreased permeability results in a lower probability of detection when using Magnetic Particle Inspection. More specifically, POD decreases because MPI testing using a permanent magnet (like that used with the permanent Yoke technique) does not allow the NDT technician to control magnetic current. As a result, the inspector may reach saturation levels, even though the material is not magnetic enough to accurately detect flaws. Overall, decreased permeability makes it difficult to effectively uncover indications, especially those that are not large or surface breaking.
The graph below demonstrates the relationship between permeability and induced magnetism based on the strength of the external magnetic field that is applied.
The probability of detecting indications with MPI testing is especially low when evaluating fatigued materials using the AC/DC or permanent Yoke technique. This is because the technique does not allow the NDT technician to control the amount of magnetization. Rather, the AC/DC or permanent Yoke technique is a one-size-fits-all method of testing.
In addition, welded and fatigued materials exhibit variances in permeability. In other words, different areas of the material (e.g. parent material, heat-affected zone, weld) will have different permeability values. Again, because it is a one-size-fits-all method, the AC/DC or permanent Yoke technique does not lend well to testing materials with varying permeability. However, there are ways to improve the probability of detection when using MPI testing.
How to increase the probability of detection with MPI Testing
While the POD for Yoke MPI testing is low, other Magnetic Particle Inspection techniques offer a higher probability of detection. In particular, MPI testing techniques that allow for control over the magnetizing force (i.e. current control) have the best probability of detection.
MPI Techniques
Several common techniques are used to induce magnetization when employing Magnetic Particle Inspection. These include:
- Prods magnetization
- Longitudinal magnetization
- Circular magnetization
- Yoke magnetization
- Multi-vector magnetization
Of these MPI testing techniques, the ones that allow for the most control over magnetic current will have the highest probability of detection for fatigued materials.
In addition to employing a more reliable technique when fatigue is present, NDT technicians who are aware of the impacts of fatigue and changes in permeability can use this knowledge to offer better results in the field. Leading NDT companies, employ knowledgeable technicians who are familiar with the implications of magnetic physics and can ensure the best probability of detection.